The cement products industry can be classified into cement asbestos and cement pipe segment. Asbestos Cement sheets (ACS) have been used in India for 70 years. Being weatherproof and corrosion resistant, these sheets are practically ageless and maintenance free, whereas metal sheets corrode and deteriorate with age and exposure. AC Sheets have also proven to be the most cost effective, easy-to-install, strong and durable roofing material for warehouse, factories, low-cost housing, and practically any structure needing a roof.
The world has no alternative to asbestos corrugated roof sheeting as an affordable hard roof. Around 50-80% of our rural population lives under thatched roof. The rural income levels are low and they can only graduate from thatched roof to asbestos cement roof sheeting. On the other side, Cement pipes find application in drinking water supply and drainage & sanitation works.
Budget Provisions:
- Basic excise duty enhanced from 10% to 12%.
- Proposal to provide Rs 15,888 crore for capitalization of Public Sector Banks, Regional Rural Banks RRB and other financial institutions including NABARD.
- Extent the scheme of capitalization of weak RRBs by another 2 years to enable all the states to contribute their share.
- Enhance provisions under Rural Housing Fund from Rs 3000 crore to Rs 4000 crore.
- A short term RRB Credit Refinance Fund is being set-up to enhance the capacity of Regional Rural Banks to disburse short-term crop loans to the small and marginal farmers. Government has proposed Rs 10000 crore to NABARD for refinancing the RRBs through this fund.
- Farmers need timely access to affordable credit. Proposal to raise the target for agricultural credit in 2012-13 to Rs 5,75,000 crore. This represents an increase of Rs 1,00,000 crore over the target for the current year.
- The interest subvention scheme for providing short term crop loans to farmers at 7% per annum will be continued in 2012-13.An additional subvention of 3% will be available to prompt paying farmers.
- Government has proposed to increase the budgetary allocation by 27% for rural drinking water and sanitation from Rs 11,000 crore in 2011-12 to Rs 14,000 crore in 2012-13.
- Proposed to enhance the allocation under Rural Infrastructure Development Fund (RIDF) to Rs 20,000 crore, in which Rs 5000 crore exclusively for creating warehousing facilities.
- To improve quality of assets and to bring about greater synergy between, Mahatma Gandhi National Rural Employment Guarantee Scheme and agriculture and allied rural livelihood is being addressed.
- The Swarnjayanti Gram Swarozgar Yojana has been restructured into National Rural Livelihood Mission to provide self-employment opportunities.
- The effective excise duty on cement has come down in general, with greater benefit for mini cement plants. However, this will not bestow any benefit to asbestos cement sheet producers, as they are cenvatable, and a pass through item.
Industry Performance:
Indian Asbestos Corrugated Sheets (ACS) sector consists of about 20 entities Industry with about 68 manufacturing across the Country. The industry witnessed modest profits in the quarter ended 2011 factoring the rise in rural income.
The aggregate of 8 companies reported net sales at Rs 1508 crore, higher by 16% in the quarter ended December 2011 on y-o-y basis. This is due to increased demand from rural people on the back of improved income with the good monsoon. But, crash in OPM by 120 bps to 11.6% limited the growth of operating profit to 5% to Rs 175 crore. However, increase in other income by 67% to Rs 10 crore led the PBIDT to grew by 7% to Rs 185 crore. Further, spurt in interest costs by 3%to Rs 31 crore followed by 9% rise in depreciation costs to Rs 51 crore and provision for taxation by 3% to Rs 32 crore restricted the net profit growth to 9% to Rs 71 crore in Q3 FY12 on y-o-y basis.
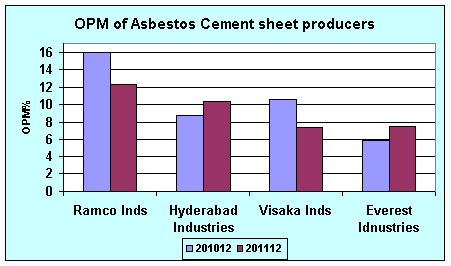
Ramco Industries net profit declined by 17% to Rs 7.1 crore
Ramco Industries, having diverse business interest of Cement Fiber Cement products, Cotton Yarn and Information technology reported 8% rise in net sales to Rs 158.62 crore on y-o-y basis during the quarter ended December 2011.This is due to increase in sales from building products segment by 15% to Rs 138.67 crore. However the sales from textiles and wind mills segments declined by 18% to Rs 20.93 crore and 12% to Rs 1.76 crore respectively. However, building products segment account 86% to the total sales and 13% by textiles segment and rest by windmills segment. But, decline in OPM by 400 bps to 12% pulled down the operating profit by 16% to Rs 20.35 crore. The decline in margins was due to increase in raw material costs as a % of adjusted sales by 900 bps to 59% coupled with the rise in employee expenses by 50 bps to 6% in Q3 FY12 on y-o-y basis. Further, spurt in interest and depreciation costs led the net profit to decline by 17% to Rs 7.1 crore though the tax provision costs eased by 10% on y-o-y basis.
Visaka Industries to scale up the Sambalpur unit capacity to 2.16 lakh tonnes per annum
Visaka Industries, which is engaged in the manufacture of fiber, cement products and synthetic blended yarn recorded net sales at Rs 170.2 crore, higher by 13% in Q3 FY12 on y-o-y basis. This is due to increase in building product segment sales by 14% to Rs 132.29 crore and 9% rise in synthetic blended yarn sales. But crash in OPM by 320 bps to 7.3% on the back of increase in raw material costs as % of adjusted sales by 143 bps to 61% coupled with the rise in other expenses by 162 bps to 14% pulled down the operating profit by 21% to Rs 12.59 crore. Adding to this, increase in interest costs led the net profit to fall by 42% to Rs 4.38 crore limited by fall in provision for taxation costs by 43% to 2.15 crore.
Being competitive on potential for Asbestos Cement Sheets (ACS) in the country, Visaka Industries has added a new unit at Sambalpur in Orissa with a capacity of 1,10,000 tonnes per annum (tpa). Now the company plans to further expand the Sambalpur unit capacity to 2.16 lakh tpa in a phased manner. The Company had earlier acquired about 33 acres of land in Rengali District, Sambalpur, Orissa. The entire project cost is estimated at Rs 41 crore.
As of now, the company's overall capacity has gone up by 20% from 6,50,000 tpa in last fiscal year with the installation of Sambalpur plant. The capacity utilization of sambalpur unit is likely to be about 50% during the quarter ended March 2012 and is likely to reach 75% in 2012-13. However, the overall capacity utilization of the company is expected to ease in the coming period with the new capacity additions.
Hyderabad Industries commenced production of fiber cement sheets of 90,000 MT/annum
Hyderabad Industries which is engaged in the production and distribution of Fibre Cement Sheets, Aerocon Panels, AAC Blocks, Material Handling and Processing Plant and Equipment and Thermal Insulation Products (Refractories) reported net sales at Rs 193.51 crore, higher by 15% in Q3 FY12 on y-o-y basis on the back of 17% rise in sales to Rs 185.57 crore from building products segment which account about 95% to the total sales. But the thermal segment sales declined by 15% to Rs 8.4 crore, which accounts the remaining 5% to the total sales. Its OPM improved by 164 bps to 10% on reduction in raw material costs as % adjusted sales and led the operating profit to grow by 36% to Rs 20.21 crore. Therefore, with the increased sales and improved margins coupled led the net profit to grew by 60% to Rs 10.16 crore on y-o-y basis.
HIL has set up a 3.6 MW wind power project in Gujarat and a 1.25 MW wind power project in Tamil Nadu.Both the AAC block plants in Gujarat and Tamil Nadu captively consume the electricity generated from the wind power projects and providing huge revenue potential. The Company is planning several wind power projects in the states of Gujarat and Rajasthan, with a target of achieving 30 MW capacity by 2015. The company is currently focusing on creating a domestic market for non-asbestos based building products, including tiles, walls and ceiling along with expanding its AC sheet manufacturing capacity. Besides, it is also expanding its flat product line involving cement –based products that are suitable to replace plywood in certain building products.
Company might begin to manufacture some of non-asbestos products locally in two years while other products could take about four years. As part of this strategy, company is open to have joint venture with companies that have strengths in this sector even overseas company too.
Company, which has 12 production lines in nine pants across India, has commenced commercial production of an additional line at its fiber cement sheets manufacturing plant at SIDA, Sathariya, Jaunpur district, Uttar Pradesh with an installed capacity of 90,000 MT/annum at a cost of Rs 50 crore. With this, the total installed capacity of the Company's fiber cement sheet manufacturing plant in Sathariya is 1,80,000 MT per annum.
Everest Industries plans to set up fiber cement plant of capacity 1,00,000 MT pa
Everest Industries is into manufacturing of fiber based cement products, such as sheets for roofing and interiors as well as non-asbestos flat sheets for varied application including pre-fab housing. The net sales for the quarter ended December 2011 increased by 16% to Rs 208.44 crore on y-o-y basis on increase in steel buildings sales by 30% to Rs 57 crore and 12% jump in building products sales to Rs 153.24 crore. The rise in net sales led the OPM to improve by 170 bps to 7.5%, which in turn pulled up the operating profit by sharp 50% to Rs 16 crore. However, rise in employee expenses by 400bps to 20% and increase in other expenses by 30bps to 20% set the PBIDT to fall by 7% to Rs 17 crore. Further, spurt in interest costs, provision for depreciation and taxation costs led the net profit to decline by sharp 27% to Rs 7.3 crore on y-o-y basis. Everest Industries proposed to acquire land and set up plant for manufacture of Fiber Cement Products in Orissa at a cost of Rs 50 crore approximately for manufacture of Fibre Cement Products with a capacity of 1,00,000 MT p.a.
Raw material scenario
The raw materials constitute almost 45-50% of the total expenditure. AC cement sheets are made with a mix of chrysotile fibers (about 8-9%), cement and other raw materials like - Pozzolona Ash and Ordinary Portland Cement. Over 90% of asbestos fibre imports are used in the AC sheet and pipe production, with increased environmental consciousness leading to ban on asbestos mining in most part of India.
With 2004-05 as a base, prices of Grey Cement and asbestos corrugated sheets price index grew by 6% and 7% during Feb 2012 on y-o-y basis. Similarly, cost of other inputs like slag asbestos fibre etc have also increased. Moreover, with the enhancement of the excise duty from 10% to 12% in the Budget 2012-13, the ACS price index is likely to increase in the coming period.
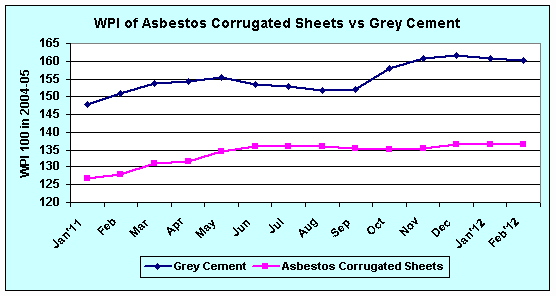
Currently, Asbestos Corrugated sheets prices are at new highs and are likely to grow further high on the back of increased input prices and improved demand from rural India. Hence, the increased price realizations and volumes would thereby improve the profitability of the sector in the coming quarters.
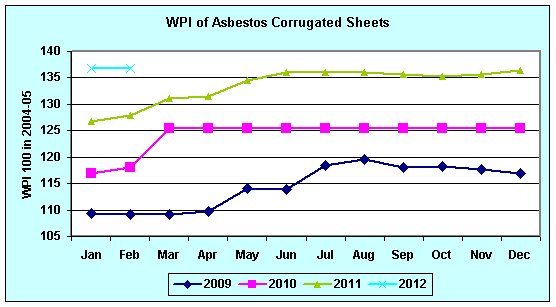
Outlook:
The Cement products industry is expected the continue the growth of 10% largely driven by rural India in the future. Indeed, Government is keen to improve living standards of Rural India. Hence, the proposals made by the government in the Union Budget 2012-13 like capitalization of Rural banks, allocation for Rural Housing Fund, providing RRB Credit Refinance Fund, agricultural credit and interest subvention scheme to the farmers, allocation for rural drinking water and sanitation, Rural Infrastructure Development Fund are likely to increase the livelihood of rural India. Besides, the various Government schemes and plans such as Mahatma Gandhi National Rural Employment Guarantee Scheme, National Rural Livelihood Mission are likely to improve further the purchasing power of rural India and thereby drive the demand for Asbestos cement sheets.
The sector succeeded in improving the selling price of Asbestos Corrugated Sheets to Rs 150 per meter, higher by 11% from Rs 135 per meter in April 2011. However, the industry was yet to effect hike after Union Budget 2012-13, despite hike in excise and service tax from 10% to 12%. The hike, if any, will depend on the growth in demand, and absorption of the hikes effected already. With most input costs, including cement, going up, the sector will start feeling the pressure on margins from early next fiscal, if the ACS prices are not hiked. But for the current quarter ending March 2012, they are expected to report decent growth in revenues and profits.
|